PROCESO DE FOSFATIZADO
Introducción
Los recubrimientos de conversión son aquellos que se producen por efecto de una conversión química de la superficie de un sustrato metálico, y cuya finalidad es la de proteger al sustrato de la corrosión o modificar sus propiedades de adherencia.
Uno de los procesos más comunes que involucra la formación de un recubrimiento de conversión, es el fosfatizado de metales.
Este es un proceso, mediante el cual se forma una capa insoluble de fosfato sobre un sustrato de hierro, zinc o aluminio.
Para la mayoría, la importancia en la aplicación de un recubrimiento fosfatico, recae en el pre tratamiento del sustrato antes de pintar. Así todos los artículos fabricados y provenientes de hojas metálicas, serán tratados en esta forma.
El rol del recubrimiento fosfatico, es proveer un sustrato de calidad como:
- 1. Medio de retención de aceites anticorrosivos para protección del sustrato.
- 2. Base para mejora del anclaje de la pintura en sustratos que requieren ser pintados y para prevención de la corrosión bajo la pintura.
- 3. Medio de retención de aceites lubricantes para procesos de maquinado.
La contribución del fosfato en la promoción de adhesión, puede describir los siguientes factores:
- 1. Un incremento en el área superficial del substrato, llevándolo a la posibilidad de un incremento en la adhesión.
- 2. Absorción de pintura en microfisuras en el recubrimiento antes de la polimerizacion, dando mejor ínter penetración de ambos recubrimientos.
- 3. Reacciones químicas entre resinas insaturadas y cristales de fosfato.
Los recubrimientos fosfáticos para la adhesión de la pintura recaen en dos categorías distintas.
- 1. Fosfato de hierrro amorfo.
- 2. Fosfato de zinc cristalino.
Generalmente se habla de la elección entre un fosfato de hierro y un fosfato de zinc, la elección de alguno de estos dos procesos va a estar determinado por el uso final de los artículos a ser tratados. Donde el medioambiente es hostil, ej. Autos, tractores, maquinas lavadoras, etc. el proceso de fosfato de zinc es el preferido, pero para los productos para medio ambientes menos severos, muebles de oficina, soportes de tubos fluorescentes, etc., el proceso de fosfato de hierro es el mas adecuado.
La mayor promoción de las propiedades de flexibilidad y adhesión son también requeridas si el artículo será conformado después del pintado.
Proceso de fosfato de hierro
Este recae en dos distintos grupos:
- 1. el proceso usado con limpiadores separados en cinco o seis etapas.
- 2. el proceso usado con limpiadores recubridores usados en tres o cuatro etapas.
1.- Proceso con limpiadores separados
Este esta basado en un fosfato de sodio o de amonio con acelerantes y producen recubrimientos en un rango de 0,3 a 0,6 g/m2.
Una secuencia típica de operación podría ser la siguiente:
- 1. Desengrase alcalino: 1 o 2 minutos por spray o 2 a 4 minutos por inmersión.
- 2. Enjuague: 30 segundos por spray o 1 minuto por inmersión.
- 3. Fosfato: 1 a 2 minutos por spray o 2 a 4 minutos por inmersión.
- 4. Enjuague: 30 segundos por spray o 1 minuto por inmersión.
- 5. Sellado: 30 segundos por spray o 1 minuto por inmersión.
Las temperaturas operativas pueden variar entre 30º C y 75º C dependiendo de las concentraciones. La apariencia del recubrimiento esta influenciada por los acelerantes empleados; la modificación de las formulaciones esta disponible para el tratamiento de distintas aleaciones de aceros, aceros galvanizados y aluminio. El enjuague final con un sellador orgánico o crómico es un aporte importante del proceso. Este puede ser seguido por un enjuague final de agua desionizada.
Los procesos con Fosfato de hierro operan a una baja acidez y con una fuerza más baja que otros procesos de fosfatos. Una consecuencia de esto es que es posible incorporar agentes activos a la superficie y otros agentes de limpieza y llevar a cabo la limpieza y la conversión en una simple operación, y también por spray.
En la practica un proceso de doble propósito seria:
- 1. Desengrase/fosfatado 1 minuto spray.
- 2. Desengrase/fosfatado 1 minuto spray.
- 3. Enjuague 30 segundos spray.
- 4. Sellado 30 segundos spray.
El primer paso es mayormente el de limpieza, y el paso 2 es el de tratamiento. Cuando el paso 1 se contamina con la suciedad removida, esta es descartada y la solución del paso 2 es transferida a la etapa 1, y se hace una nueva solución en la etapa 2. Esto se hace para que la etapa 2 quede libre de contaminación. Esto no es posible hacerlo en una etapa, sin los frecuentes descartes.
Los fosfodesengrases pueden ser usados por inmersión, pero en algunos es necesario la agitación para asegurar una adecuada limpieza.
Los fosfodesengrases convencionales son productos en polvo o líquidos.
Las temperaturas operativas están en el rango de los 35-80 C con espesores de 0.2 – 0.4 g/m2.
Mas recientemente han sido introducidas las soluciones liquidas, las cuales se usan en conjunción con equipos automáticos, los cuales son capaces de operar por spray a temperaturas más bajas.
La cuestión de la apariencia optima del recubrimiento de fosfato de hierro es materia de cierta controversia.
El recubrimiento puede ser iridiscente, azul o gris dependiendo de un numero de factores que incluyen el ph, los acelerantes y los espesores.
De todas maneras con la amplia variedad de pinturas y procesos de fosfatos disponibles, es peligroso generalizar, y la elección de un proceso requiere del conocimiento individual sobre la base de un programa de evaluación.
El uso de los fosfodesengrases es algo incuestionable; los mejores resultados de los procesos de fosfato de hierro son obtenidos con etapas de limpieza separada. , esto no quiere decir que los fosfodesengrases no sean adecuados para algunas aplicaciones.
Proceso de Fosfato de Zinc
Para el proceso de inmersión, los procesos con acelerantes de nitritos y nitratos, son comúnmente los mas empleados.
Un proceso típico operaria a 65 C y produce una capa de recubrimiento en el orden de 3.0-7.0 g/m2
Los procesos de fosfato de zinc no modificados, son adecuados para un amplio rango de pinturas al solvente, pero sufren una desventaja, ya que la capa del recubrimiento y la estructura cristalina están muy afectadas por el método de limpieza empleado.
Los desengrases altamente alcalinos y de ataque ácido, ambos tienden a producir rugosidad, que se traduce en recubrimientos gruesos con efectos adversos para el brillo y la adhesión.
Donde el uso de algunos de estos limpiadores no puede ser descartado, sus efectos adversos pueden ser eliminados o minimizados por el uso de activadores.
La mejor solución es la incorporación de agentes refinadores del recubrimiento, en el baño de fosfato.
Mientras que los agentes refinadores orgánicos tienen un efecto limitado, el mas usado es el método de modificación química del baño, con la incorporación de calcio como recubrimiento metálico.
El recubrimiento fosfatico de zinc calcio es menos rugoso que un recubrimiento normal de fosfato de zinc, y es también menos afectado por los métodos de limpieza.
Los procesos de fosfato de zinc modificado con calcio, por inmersión, son usados con acelerantes de nitritos y operan en general de una forma similar al proceso típico de fosfato de zinc.
Una secuencia operativa tipica, puede ser la siguiente:
- 1. desengrase alcalino.
- 2. enjuague.
- 3. activación.
- 4. enjuague.
- 5. fosfato.
- 6. enjuague.
- 7. sellado.
- 8. secado.
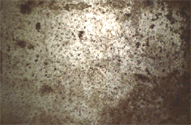
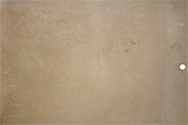
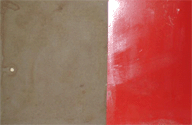
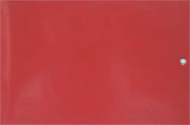
Proceso por spray
Esta es un área donde los cambios en la tecnología ha tomado lugar considerablemente en los años recientes, trayendo consigo cambios en la tecnología del pintado, presiones medioambientales, y conservación de la energía.
Por muchos años, el proceso de fosfato de zinc con acelerantes nitritos, cloratos, o una combinación de ambos, fue empleado operativamente a 45-60 C por 1-2 minutos produciendo capas de recubrimientos de 1.6 – 3.0 g/m2.
Como los procesos son todavía empleados en conjunción con pinturas al solvente y las viejas clases de electropinturas anodicas, su uso ha mostrado una dramática baja a través de los últimos diez años.
El proceso de fosfato de zinc modificado fue desarrollado en USA para uso en la ind. Automotriz, donde se usaban cant. significativas de acero galvanizado. Este contiene en su composición Nikel y es usado ampliamente aun en USA.
El aumento en los precios de la energía a mediados de los 70`s, demostró un nuevo interés en los procesos de baja temperatura.
Acompañado de pruebas con desengrases de baja temperatura, los procesos de spray a baja temperatura fueron desarrollados usando fosfato de zinc modificado con manganeso y acelerantes, operando alrededor de los 30 C. Este proceso ha tenido un aceptable éxito particularmente en UK e Italia.
Los estrictos limites para el volcado de los efluentes, han demandado para este tipo de procesos un volcado cero, y dicho sist. ha sido desarrollado en Alemania.
Este proceso usa como acelerante peróxido de hidrogeno, el cual es neutralizado con carbonato de zinc.
Así los prod. obtenidos, son agua, oxigeno y dióxido de carbono, siendo los iones de zinc y fosfato los que se arrastran a los enjuagues, los cuales son fácilmente removidos por precipitación, y el agua del enjuague ser reciclada.
También los nitritos son todavía ampliamente usados como acelerantes en los sist. de spray, pero estos cuentan con algunas desventajas:
- 1. Son de baja estabilidad, y se pierden cuando el proceso no esta en marcha.
- 2. Como resultado de la descomposicion del nitrito, los óxidos corrosivos de nitrógeno, pueden acumularse en el túnel de spray y causar decoloraciones y perdida de brillo.
- 3. Los mismos óxidos pueden acumularse en el ámbito de la fabrica o el medio ambiente, y tornarse peligrosos para la salud, y el mantenim. De los operarios.
- 4. enjuague.
- 5. fosfato.
- 6. enjuague.
- 7. sellado.
- 8. secado.
Por estas razones se buscaron nuevas alternativas de acelerantes para los sistemas por spray.
Un nuevo sistema de acelerantes, basado en la combinación de distintos productos, ha sido introducido y probado con éxito en operaciones a temperaturas medias 45 C y bajas 30C.